What is the Gravity Pipeline Project?
Silicon Valley Clean Water’s long-anticipated gravity pipeline project continues to progress with site work and shaft construction activities in anticipation of delivery next July of a tunnel boring machine (TBM) from Germany. The $18.2 million TBM being built by Herrenknecht Tunneling Systems of Schwanau will be disassembled and shipped to Redwood City through one of four ports in Northern California and then reassembled on site.
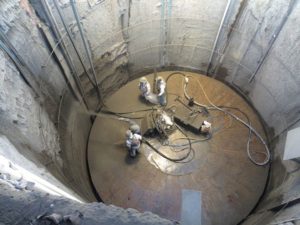
Tunnel launch shaft sitework began in September northeast of the intersection of Shoreway Road and Redwood Shores Parkway/Holly Street intersection. Site work involves grading and general preparation for the shaft and tunneling construction activities that are planned to start in November 2019 and continue through the spring of 2022.
The gravity pipeline, which the TBM will install from the north edge of Inner Bair Island to the new facilities at the front of the treatment plant at 1400 Radio Road, is a major component of SVCW’s Regional Environmental Sewer Conveyance Upgrade (RESCU) program. RESCU improvements will enable the safe and reliable transport of wastewater from four-member agencies’ collection systems to the treatment plant.
The first tunnel section to be constructed will be located between the Shoreway Road/Redwood Shores Parkway TBM Launch Shaft and the Inner Bair Island Inlet Shaft. This tunnel section will be located under Redwood Shores Parkway (Holly Street), Skyway Road, the San Carlos Airport property (adjacent to, not under, the runways and taxiways), and Pulgas Creek, where it will connect to the recently completed 48-inch force main pipe on Inner Bair Island. This tunnel section will be approximately 5,200 feet in length (slightly less than a mile) and will be installed 20 to 35 feet below ground.
The second tunnel section to be constructed will be located between the TBM Launch Shaft and the TBM Retrieval Shaft located at the SVCW treatment plant, with most of the tunnel located beneath the Redwood Shores Parkway public right-of-way. This tunnel section will be approximately 12,400 feet in length (about 2.4 miles) and will be installed roughly 35 to 60 feet below ground level (to the top of the tunnel).
Tunneling is used as an alternative to open cut methods. Tunneling using TBMs has the advantages of limiting the disturbance to the surrounding ground and allowing long distances between shafts. This significantly reduces the negative impact of construction to the public and cost of construction and is suitable to use in heavily urbanized areas.
Wanting to collaborate with a contractor and designer from the project’s earliest stages, SVCW joined in a Progressive Design-Build agreement with Barnard Bessac Joint Venture, along with design engineer Arup, to design and construct the gravity pipeline. Barnard Bessac JV and Arup are working with SVCW to take the design of the gravity pipeline project from 10 percent to 100 percent.
To ensure contractor involvement from the design phase continuing through construction, SVCW divided the contract into two stages, where Stage 1 takes the design to 60 percent, and Stage 2 brings the design to 100 percent and includes all required gravity pipeline tunnel and shaft construction.
The tunnel will be constructed using a Tunnel Boring Machine (TBM). TBMs are operated by personnel within the tunnel using real time monitoring of tunneling progress and performance. Tunnel personnel, assisted by robotics, assemble the concrete tunnel segments to construct the exterior walls of the tunnel within the front shield area of the TBM (first ~40 feet of the ~600 foot long TBM). These concrete segments, which form the tunnel walls, provide the thrust resistance required to move the TBM forward in the ground.
To construct SVCW’s tunnel, an Earth Pressure Balance Machine (EPBM) pressurized face type TBM will be used. EPBMs are sealed against external fluid pressures and prevent water from infiltrating into the tunnel. This is advantageous in soft soils below the water table, similar to the existing project soil conditions. By using this construction technique, external pressure is controlled by adjusting the rate of progress and the rate of muck removal through the screw conveyor (muck is excavated soil conditioned with Underwriters Laboratory-approved, NSF International Standard 61 compliant-biodegradable additives). The muck conveyor is located immediately behind the rotating cutting face of the machine.
The tunneling process initiates with setup of above and below ground support services needed for the tunneling operation. This includes air supply/movement, conveyors, electrical facilities. Rails for transporting segments, equipment and laborers into and out of the tunnel are also installed as the tunnel advances. Cars pulled by a locomotive on the installed rails will bring personnel, concrete segments and other supplies to the front of the TBM.
Tunnel excavation includes muck removal by use of a conveyor system. Once the muck is brought to the surface at the Airport Access Shaft, it will be removed from the site and disposed offsite (likely for use as fill at another construction site). After the first 1,000 feet, it is anticipated that approximately 70 feet of the tunnel will be excavated each day.
Once the TBM and trailing gear reaches the Inner Bair Island shaft, it will be disassembled, removed from the shaft and transported by truck back to the Airport Access Shaft. The TBM and trailing gear then will be reinstalled in the Airport Access Shaft to construct the tunnel to SVCW’s wastewater treatment plant at the end of Redwood Shores Parkway. Once the TBM and trailing gear reaches the Flow Splitter Shaft at the treatment plant, construction using the TBM will be complete and the TBM again disassembled by the contractor; this time for final removal from the site.
Following completion of the final tunnel section, the TBM and trailing gear that was used for tunnel construction will be removed in preparation for installing the carrier pipe (Gravity Pipeline).
Vertical Alignment
- Tunnel in upper layered sediments (medium stiff clays and sand layers)
- Boring or CPT every 250 feet along alignment
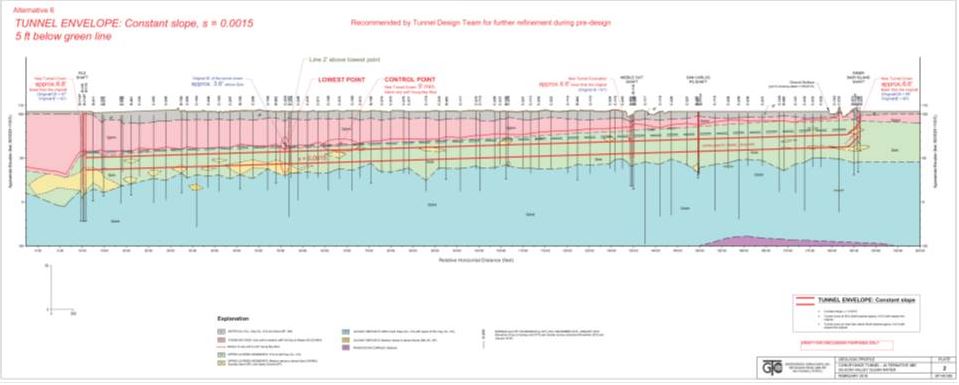
Earth Pressure Balance (EPB) Tunnel Boring Machine (TBM)
- Pressure balance is maintained at face of TBM using pressurized bulkhead and screw conveyor to keep water out of tunnel and avoid settlement
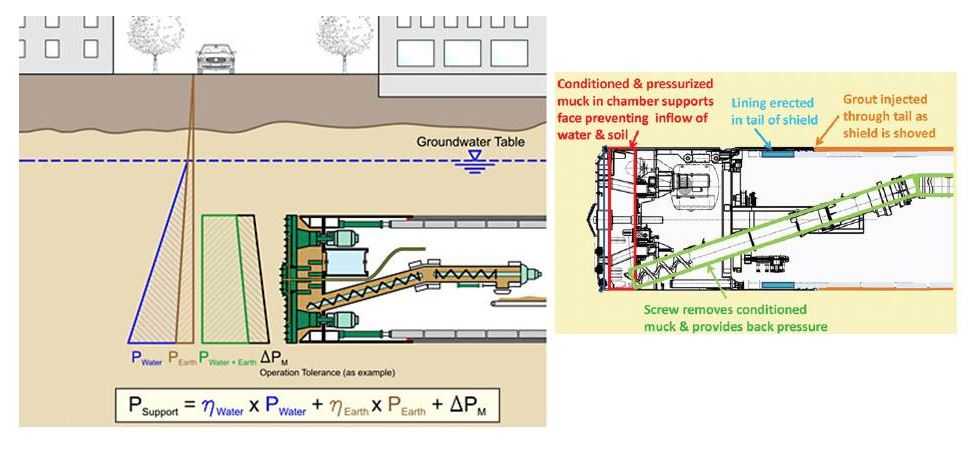
Recent Technology Improved Grout Process to make Surface Settlement Imperceptible
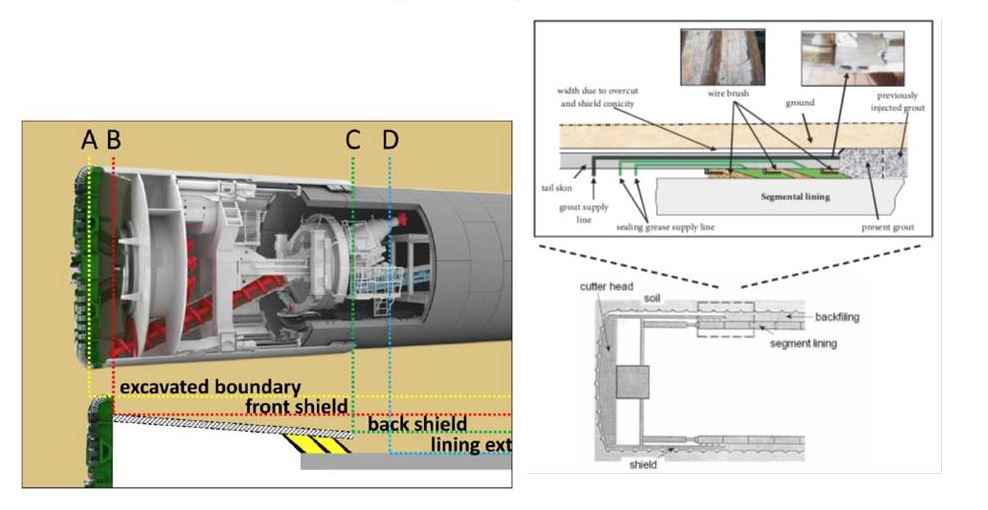
What is a tunnel boring machine (TBM) and how does it work?
A TBM is used to excavate tunnels with a circular cross section through a variety of soil strata. TBMs can bore through any soils from clay to sand to rock. Tunnel diameters can range up to 58 feet to date. TBMs have the advantages of limiting the disturbance to the surrounding ground.
The TBM for SVCW’s project will be an Earth Pressure Balance (EPB) machine. What is that and how does it work?
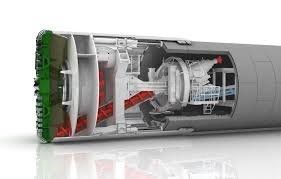
For soft, cohesive soils tunnel boring machines with earth pressure support are a preferred option. EPBs turn the excavated material into a soil paste that is used as pliable, plastic support medium. This makes it possible to balance the pressure conditions at the tunnel face, avoids uncontrolled inflow of soil into the machine, and creates the conditions for tunneling with minimum settlement.
The special feature of EPBs is that they use the excavated soil directly as support medium. This method is the first choice in cohesive soils with high clay and silt contents and low water permeability, which generally describes the soil conditions in the SVCW project area. A rotating cutting wheel equipped with tools is pressed onto the tunnel face and excavates the material. The soil enters the excavation chamber through openings, where it gets mixed with the soil paste that is already there into the required texture. When the pressure of the soil paste in the excavation chamber equals that of the surrounding soil and groundwater, the necessary balance has been achieved. Explore More
When was the first EPB tunnel boring machine built?
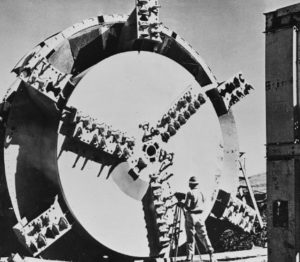
In 1964 James Robbins of Ohio developed the first compressed air tunneling machine to successfully excavate a 2.9 km (1.8 mile) long tunnel below the groundwater table in Paris, France. The design served as the genesis for the EPB TBMs we know today. EPBs originated in Japan in the 1970s. The first reported use of an EPB tunnel boring machine was in 1974 for driving an 11-foot aqueduct tunnel.
In the U.S., the first time an EPB machine was deployed was in the excavation of a 3,002-foot long tunnel in 1981 as part of the San Francisco Clean Water Program. The Channel Tunnel, the Thames Water Ring Main, sections of the London Underground, and most new metro tunnels completed in the last 20 years worldwide were excavated usig this method.
When was the first tunnel boring machine built?
The first boring machine reported to have been built was Henri-Joseph Maus’s Mountain Slicer in 1845 to dig the Fréjus Rail Tunnel between France and Italy through the Alps. Maus had it built in an arms factory near Turin. It consisted of more than 100 percussion drills mounted in the front of a locomotive-sized machine, mechanically power-driven from the entrance of the tunnel.
In the United States, the first boring machine to have been built was used in 1853 during the construction of the Hoosac Tunnel in northwest Massachusetts. Made of cast iron, it was known as Wilson’s Patented Stone-Cutting Machine, after inventor Charles Wilson.
How does a tunnel boring machine work?
A picture is worth a thousand words. These are excellent short videos that illustrate how they work:
- https://www.youtube.com/watch?v=fVidVJ30ob4&feature=youtu.be
- https://thekidshouldseethis.com/post/how-does-a-tunnel-boring-machine-work
Tell us about the company building the TBM for Silicon Valley Clean Water?
Herrenknecht AG is a German manufacturer of tunnel boring machines, headquartered in Allmannsweier, Schwanau, Baden-Württemberg. It is the worldwide market leader for heavy tunnel boring machines. Roughly two-thirds of the 5,000 employees work at the company headquarters in the installation of hydraulic and electronic components as well as final inspection. The company contains 82 subsidiaries around the world and has worked on 4,100 projects. It builds TBMs for road, railway, metro, and utilities construction.