Construction work at the Headworks Facility and Receiving Lift Station (RLS) are ongoing, with SVCW’s contractor partner, Shea Parsons Joint Venture (SPJV), finishing up with the install of the remaining RLS discharge pipes to Headworks Facility. These discharge pipes will carry wastewater flows from the RLS into the Headworks Facility when the Front of Plant (FoP) processes are ready to receive wastewater. SPJV is also working on completing the last section of pile-supported apron slab which surrounds the RLS shaft to provide support to the RLS pump discharge pipes. SPJV is also installing various electrical components and miscellaneous piping over the next few months.
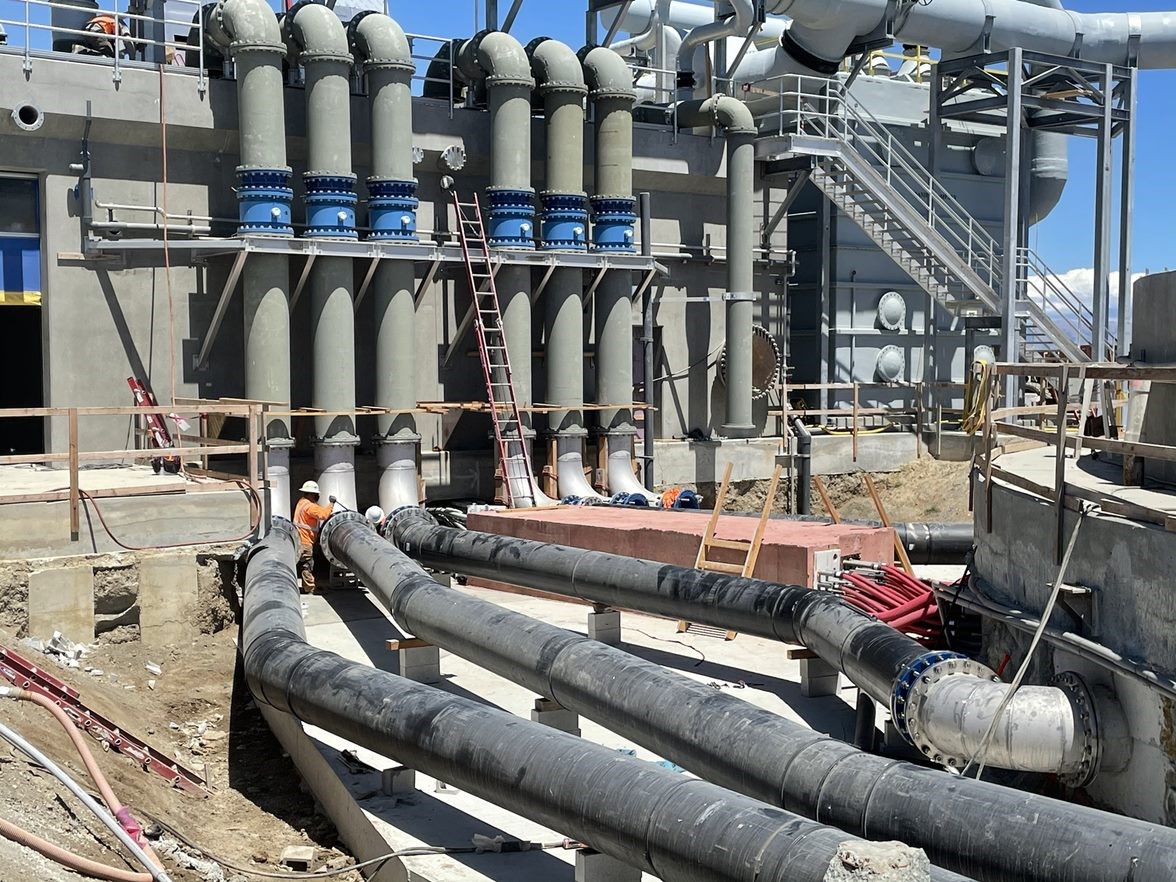
As different pieces of equipment are being installed in and around the RLS, SPJV has started working on the construction of eight RLS precast concrete roof panels. The supporting formwork and rebar for the roof panels have been prepared for two of the panels and are ready for concrete placement. Each of the remaining panels will be cast in the FoP construction work area and lifted into place when cured to preset connection points on the top of the RLS shaft. In addition to working on getting the RLS roof panels cast and set in place, SPJV is working on constructing the remaining mezzanine decks within the RLS. These mezzanine decks, when completed, will serve as the maintenance and observation platforms for SVCW’s Operations & Maintenance staff.
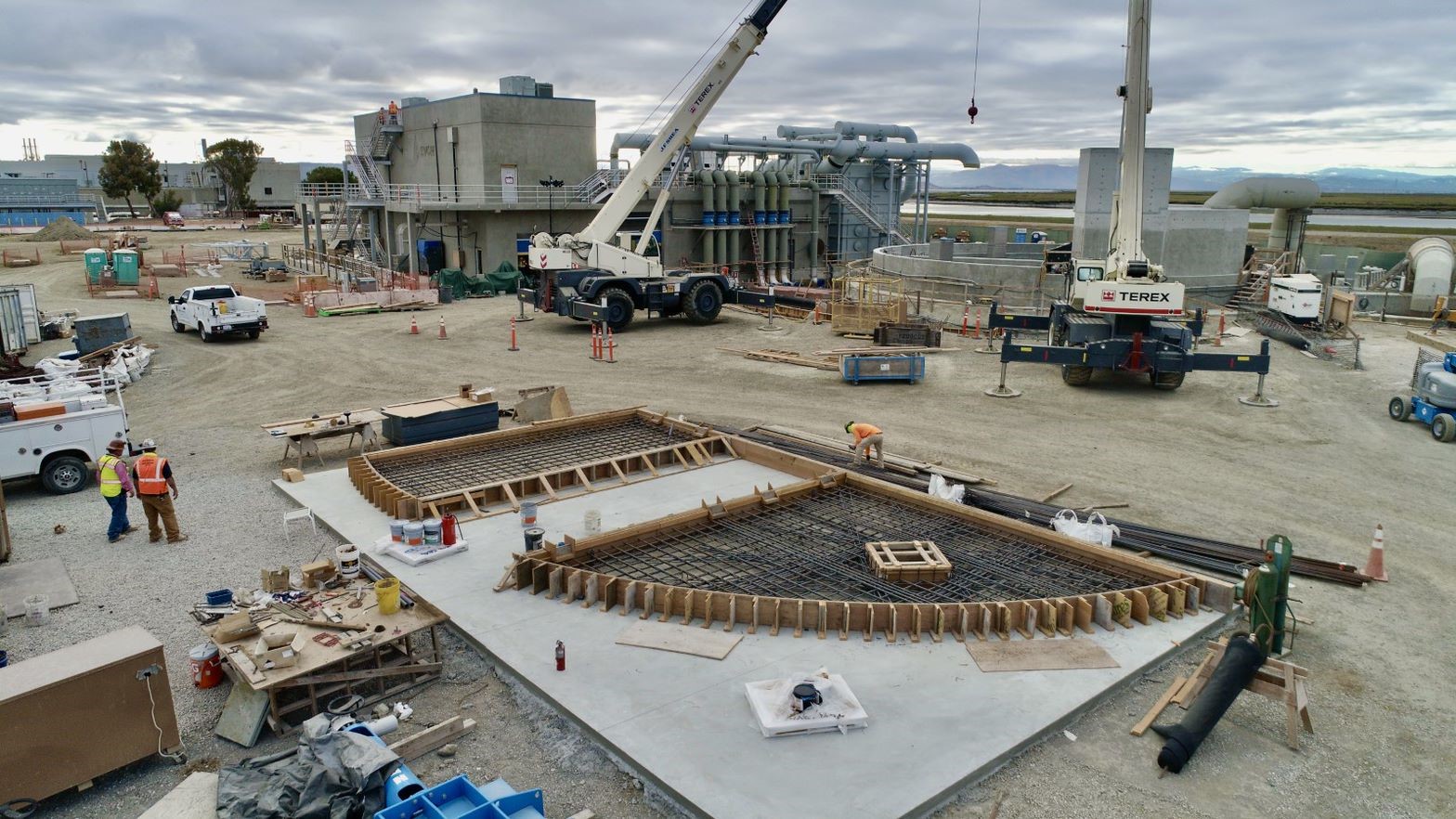
Aside from construction, SPJV has also started to prepare dry functional testing plans (i.e., no water is used for testing) for the Front of Plant equipment. Dry Functional Testing is a process of checking each piece of equipment for proper installation by the manufacturer, testing electrical connection to equipment etc. To ensure that, when ready to wet test, the systems are ready for operation. These plans are part of the scheduled process for startup and commissioning of the Headworks Facility, the RLS, and the Surge/Flow-Splitter (SFS) shaft at the Front of Plant. Once the plans for dry functional testing are completed, SPJV can move on to developing plans for wet testing, which involves using water flows (anticipated at this time to be recycled water) through the FoP equipment to test the various Front of Plant components and equipment.
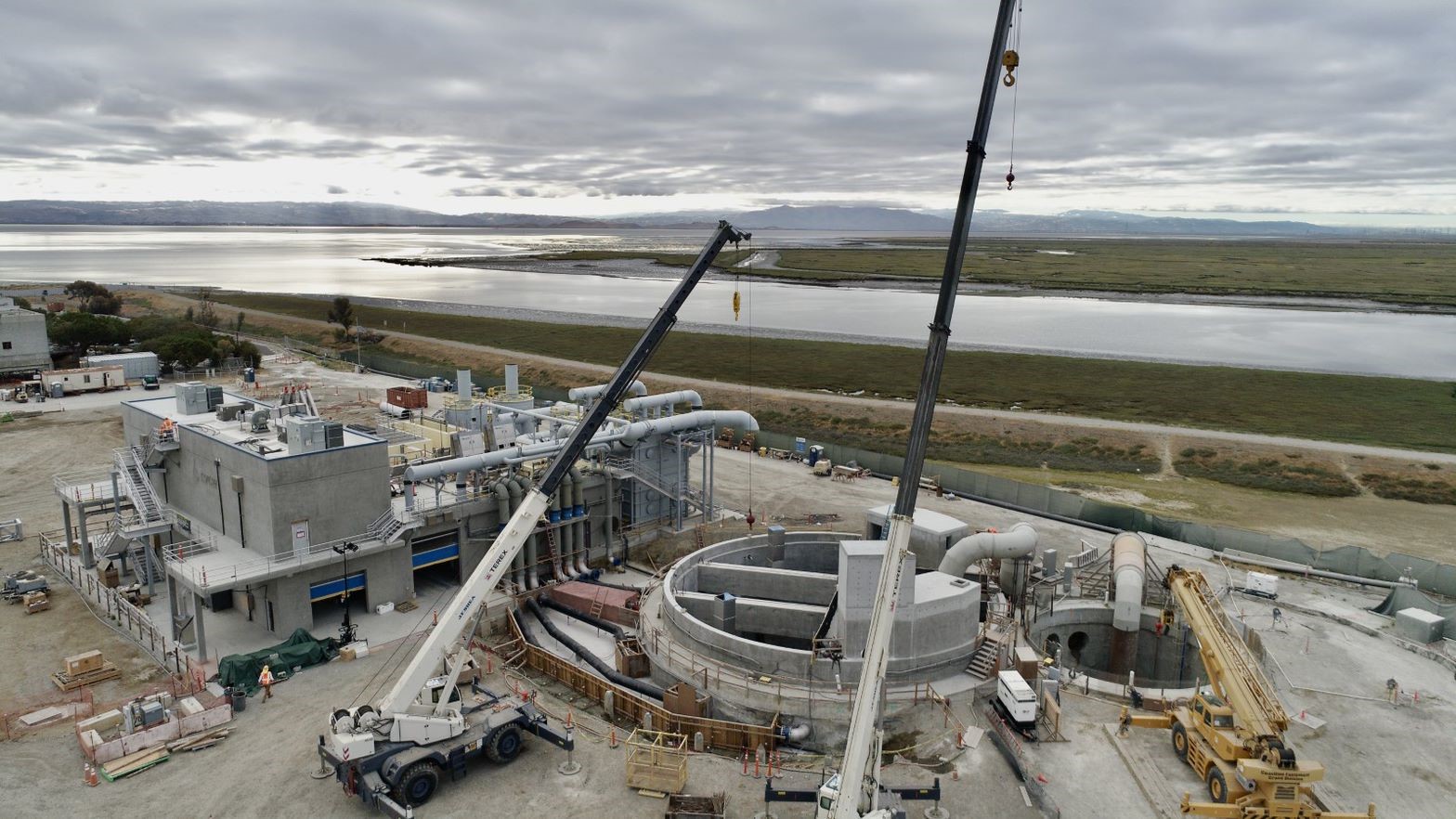